Case Study Six: The Upper Big Branch Mine Disaster
On Monday, April 5, 2010, just before 3:00 in the afternoon, miners at Massey Energy Corporation’s Upper Big Branch coal mine in southern West Virginia were in the process of a routine shift change. Workers on the evening shift were climbing aboard “mantrips,” low-slung electric railcars that would carry them into the sprawling, three-mile-wide drift mine, cut horizontally into the side of a mountain. Many day shift workers inside the mine had begun packing up and were preparing to leave, and some were already on their way to the portals. At one of the mine’s main “longwalls,” one thousand feet below the surface, a team of four highly experienced miners was operating a shearer, a massive machine that cut coal from the face with huge rotating blades. The shearer had been shut down for part of the day because of mechanical difficulties, and the miners were making one last pass before the evening shift arrived to take their places.
The Upper Big Branch Mine Disaster
Suddenly, a spark thrown off as the shearer’s blades cut into hard sandstone ignited a small pocket of flammable methane gas. One of the operators immediately switched off the high-voltage power to the machine. Seconds later, the flame reached a larger pocket of methane, creating a small fireball. Apparently recognizing the danger, the four miners on the longwall crew began running for the exit opposite the fire. They had traveled no more than 400 feet when coal dust on the ground and in the air ignited violently, setting off a wave of powerful explosions that raced through the mine’s seven miles of underground tunnels. When it was over three minutes later, 29 miners (including all four members of the longwall crew) were dead, and two were seriously injured. Some had died from injuries caused by the blast itself, others from carbon monoxide suffocation as the explosion sucked the oxygen out of the mine. It was the worse mining disaster in the United States in almost 40 years.
An evening shift miner who had just entered the mine and boarded a mantrip for the ride to the coal face later told investigators what he had experienced:
All of a sudden you heard this big roar, and that’s when the air picked up. I’d say it was probably 60-some miles per hour. Instantly black. It took my hardhat and ripped it off my head, it was so powerful.
This miner and the rest of his group abandoned the mantrip and ran for the entrance, clutching each other in the darkness. On the outside, stunned and shaken, they turned to the most senior member of their crew for an explanation. “Boys …, I’ve been in the mines a long time,” the veteran miner said “That [was] no [roof] fall…. The place blew up.”1
The Upper Big Branch Mine Disaster
(page 489)
Massey Energy Corporation
At the time of the explosion, Massey Energy Corporation, the owner and operator of the Upper Big Branch mine, was one of the leading coal producers in the United States. The company, which specialized in the production of high-grade metallurgical coal, described itself as “the most enduring and successful coal company in central Appalachia,” where it owned one-third of the known coal reserves. Massey extracted 37 million tons of coal a year, ranking it sixth among U.S. producers in tonnage. The company sold its coal to more than a hundred utility, metallurgical, and industrial customers (mostly on long-term contracts) and exported to 13 countries. In 2009, Massey earned $227 million on revenue of $2.7 billion. The company and its subsidiaries employed 5,800 people in 42 underground and 14 surface mines and several coal processing facilities in West Virginia, Kentucky, and Virginia.
Massey maintained that it brought many benefits to the nation as a whole and to the Appalachian region. The coal industry in the United States, of which Massey was an important part, provided the fuel for about half of the electricity generated in the United States, lessening the country’s reliance on imported oil. The company provided thousands of relatively well-paying jobs in a region that had long been marked by poverty and unemployment. Economists estimated that for every job in the coal industry, around three and a half jobs were created elsewhere. The company donated to scholarship programs, partnered with local schools, and provided emergency support during natural disasters, such as severe flooding in West Virginia in May 2009. “We recognize that it takes healthy and viable communities for our company to continue to grow and succeed,” Massey declared in its 2009 report to shareholders.
The Upper Big Branch Mine Disaster
But critics saw a darker side of Massey. The company was one of the leading practitioners of mountaintop removal mining, in which explosives were used to blast away the tops of mountains to expose valuable seams of coal. The resulting waste was frequently dumped into adjacent valleys, polluting streams, harming wildlife, and contaminating drinking water. In 2008, Massey paid $20 million to resolve violations of the Clean Water Act, the largest-ever settlement under that law. In an earlier incident, toxic mine sludge spilled from an impoundment operated by the company in Martin County, Kentucky, contaminating hundreds of miles of the Big Sandy and Ohio rivers, necessitating a $50 million cleanup. Worker safety was also a concern. An independent study found that Massey had the worst fatality rate of any coal company in the United States. For example, in the decade leading up to the Upper Big Branch disaster, Peabody Coal (the industry leader in tons produced) had one fatality for every 296 million tons of coal mined; Massey’s rate was one fatality per 18 million tons—more than 16 times as high.
Donald L. Blankenship
At the time of the Upper Big Branch mine disaster, the chief executive officer and undisputed boss of Massey Energy was Don Blankenship. A descendant of the McCoy family of the famous warring clans the Hatfields and the McCoys, Blankenship was raised by a single mother in a trailer in Delorme, a railroad depot in the coalfields of West Virginia. His mother supported the family by working 6 days a week, 16 hours a day, running a convenience store and gas station. Michael Shnayerson, who wrote about Blankenship in his book, Coal River, reported that the executive had absorbed from his mother the value of hard work—as well as contempt for others who might be less fortunate. “Anyone who didn’t work as hard as she did deserved to fail,” Shnayerson wrote. “Sympathy appeared to play no part in her reckonings.”2
(page 490)
Blankenship graduated from Marshall University in Huntington, West Virginia, with a degree in accounting. As a college student, he worked briefly in a coal mine to earn money for tuition. In 1982, at age 32, he returned to the coalfields to join Massey Energy, taking a job as an office manager for a subsidiary called Rawls. Soon after, Massey announced it intended to spin off its subsidiaries as separate companies and re-open them as nonunion operations. The United Mine Workers, the union that then represented many Massey workers, struck the company. Jeff Goodell, a journalist who profiled Blankenship in Rolling Stone, described the young manager’s technique for defeating the union at Rawls:
The Upper Big Branch Mine Disaster
Blankenship erected two miles of chain link fence around the facility, brought in dogs and armed guards, and ferried nonunion workers through the union’s blockades. The strike, which lasted more than a year, grew increasingly violent—strikers took up baseball bats against the workers trying to take their jobs, and a few even fired shots at the scabs. A volley of bullets zinged into Blankenship’s office and smashed into an old TV…. For years afterward, Blankenship kept the TV with a bullet hole through it in his office as a souvenir.3
The union’s defeat at Massey (by 2010, only about 1 percent of Massey’s workers were union members, all of them in coal preparation plants rather than mines) contributed to the overall decline of the United Mine Workers in the coalfields. In the 1960s, unions represented nearly 90 percent of the nation’s mine workers; by 2010, they represented just 19 percent.
Blankenship quickly moved through the management ranks. In 1990, only eight years after he joined the company, he became president and chief operating officer of the Massey Coal Company and in 1992 was promoted to CEO and chairman. (The company was renamed Massey Energy in 2000 when it separated from its parent, Fluor Corp.) By some measures, he was a successful CEO. Between 2001, the first full year of Massey’s in-dependent operation, and 2009, annual revenue increased from $1.2 billion to $2.7 billion. During this period, employment rose from around 3,700 to 5,800. Blankenship more than doubled the company’s coal reserves, mainly through acquisitions of smaller firms. Massey shareholders, like all investors, were buffeted by the extreme volatility of the stock market during the 2000s. Nevertheless, an investor who purchased $10,000 worth of Massey stock in December 2004 would have a holding valued at $12,800 in December 2010—a rate of return close to that of the coal industry as a whole during this period.4
As CEO, Blankenship developed a reputation as a hands-on, detail-oriented manager. He lived in the coalfields and ran the company out of a double-wide trailer in Belfry, Kentucky, just over the West Virginia line. He signed off on all hires, all the way down to janitors. One manager expressed amazement when he learned that the CEO would have to approve a tankful of gasoline for his truck. Managers were required to fax production figures to Blankenship every half hour. Red phones connected mine managers directly to the CEO. “If the report was late or the numbers weren’t good, or the mine was shut down for any reason,” Shnayerson reported, “the red phone would ring. The terrified manager would pick it up to hear Mr. B demanding to know why the numbers weren’t right.”5 Blankenship told an interviewer, “People talk about character being what you do when no one else is looking. But the truth of the matter is character is doing that which is unpopular if it’s right, even if it causes you to be vilified.”6
(page 491)
As CEO, Blankenship maintained a laser focus on productivity. In 2005, he sent a memo titled “RUNNING COAL” to all Massey underground mine superintendents that stated:
If any of you have been asked by your group presidents, your supervisors, engineers, or anyone else to do anything other than run coal (i.e., build overcasts, do construction jobs, or whatever) you need to ignore them and run coal. This memo is necessary only because we seem not to understand that coal pays the bills.
A week later, after this memo had been widely circulated, he followed up with another one which referred to the company’s S-1, P-2 (safety first, production second) program. He wrote: “By now each of you should know that safety and S-1 is our first responsibility. Productivity and P-2 are second.”
The Upper Big Branch Mine Disaster
Executive Compensation
Blankenship was well compensated for running Massey. As shown in Exhibit A, his total compensation in 2009 was almost $18 million; this was up from $11 million in 2008 and $9 million in 2007. Blankenship’s base salary in all three years was close to $1 million. By far the greatest proportion of his total pay came from a performance-based incentive system established by Massey’s board of directors. In its filings with the SEC, the board described its philosophy of compensation this way:7
We compensate our named executive officers in a manner that is meant to attract and retain highly qualified and gifted individuals and to appropriately incentivize and motivate the named executive officers to achieve continuous improvements in company-wide performance for the benefit of our stockholders.8
Exhibit A Don Blankenship, Total Compensation 2007–2009, in Dollars
Note: “Other” includes personal use of company cars, aircraft (Challenger 601 corporate jet), housing, and related costs and services.
Source: Massey Energy 2010 Proxy, “Compensation Discussion and Analysis” and “Compensation of Named Executive Officers.”
(page 492)
Accordingly, the compensation committee of the board established an incentive plan for Massey’s CEO. (Similar plans were in place for other senior executives as well.) The plan set specific performance measures for “areas over which Mr. Blankenship was responsible and positioned to directly influence outcome.” These areas, and the proportion of his incentive compensation based on them, are shown in Exhibit B.
The Upper Big Branch Mine Disaster
Exhibit B Incentive Compensation Plan for Massey Energy’s CEO, 2009
The calculation of incentive plan compensation was based on achievement of specific targets in these areas:
EBIT (earnings before interest and taxes) -15%
Produced tons – 15%
Continuous miner productivity (feet/shift) – 5%
Surface mining productivity (tons/man-hour) – 5%
Environmental violations (% reduction) – 10%
Fulfillment of contracts – 15%
Nonfatal days lost due to injury and accident (% reduction) – 10%
Identification of successor – 5%
Employee retention – 15%
Diversity of members – 5%
Source: Massey Energy 2010 Proxy.
Note: A “continuous miner” is a large machine that extracts coal underground.
The Upper Big Branch Mine Disaster
By one estimate, in the 10 years leading up to the disaster Blankenship received a total of $129 million in compensation from Massey.9 “I don’t care what people think,” he once said during a talk to a gathering of Republican Party leaders in West Virginia, speaking of himself in the third person. “At the end of the day, Don Blankenship is going to die with more money than he needs.”10
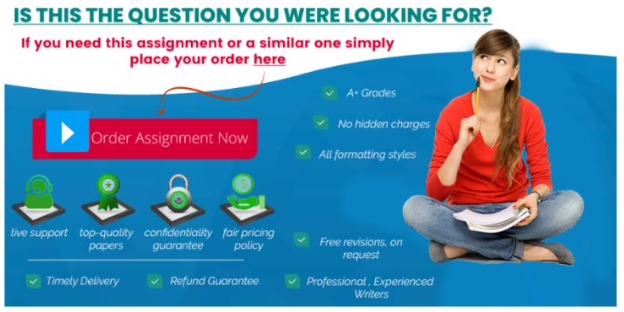
Government Regulation of Mining Safety and Health
Coal mining had always been a hazardous occupation. Methane gas, an odorless and colorless by-product of decomposing organic matter that was often present alongside coal, was highly flammable. Methane explosions had contributed to the deaths of more than 10,000 miners in the United States since 1920. To mine safely, methane levels had to be constantly monitored, and ventilation systems had to be effective enough to remove it from the mine. Coal dust itself—whether on the floor or other surfaces, or suspended in the air—was also highly flammable. The standard practice was to apply layers of rock dust (crushed limestone) over the coal dust to render it inert. In addition to the ever-present danger of fire, miners had long contended with the threat of collapsing roofs and walls, dangerous mechanical equipment, and suffocation. Miners often developed coal workers’ pneumoconiosis, commonly called black lung, a chronic, irreversible disease caused by breathing coal dust. (Black lung was preventable with proper coal dust control.)
(page 493)
Health and safety in the mining industry had long been regulated at both the federal and state levels. Over the years, lawmakers have periodically strengthened government regulatory control, mostly in response to mining disasters.
· In 1910, following an explosion at the Monongah mine in West Virginia in which 362 men died, Congress established the U.S. Bureau of Mines to conduct research on the safety and health of miners.
· The Federal Coal Mine Health and Safety Act, known as the Coal Act—which passed in 1969 after the death of 78 miners at the Consol Number 9 mine in Farmington, West Virginia—greatly increased federal enforcement powers. This law established fines for violations and criminal penalties for “knowing and willful” violations. It also provided compensation for miners disabled by black lung disease.
The Upper Big Branch Mine Disaster
· The 1977 Mine Act further strengthened the rights of miners and established the Mine Safety and Health Administration, MSHA (pronounced “Em-shah”) to carry out its regulatory mandates. The law required at least four full inspections of underground mines annually.
· Then in 2006, after yet another string of mine tragedies focused public attention on the dangers of mining, Congress passed the Mine Improvement and New Emergency Response Act, known at the MINER Act. This law created new rules to help miners survive underground explosions and accidents.11
States like West Virginia that had significant mining industries also had their own regulatory rules and agencies.
Although MSHA was empowered to inspect mines unannounced and to fine operators for violations, the agency had limited authority to shut down a mine if a serious problem was present or if the operator refused to pay its fines. Criminal violations of mine safety laws were normally considered misdemeanors rather than felonies.
Over time, fatalities in the industry had declined. At the turn of the 20th century, around 300 to 400 miners died every year in the nation’s coal mines; by the 1980s, this number had dropped to less than 50. Injuries and illnesses had also dropped. In part, these declines reflected tougher government regulations. They also reflected the rise of surface mining (mostly in the western United States), which tended to be safer, and the emergence of new technologies that mechanized the process of underground mining. The unionization of the mining industry had also given workers a greater voice and the right to elect safety representatives in many workplaces.
The Upper Big Branch Mine
Massey had bought the Upper Big Branch mine in 1993 from Peabody Coal. It was a particularly valuable property because its thick coal seam produced the high-grade metallurgic coal favored by utilities and the steel industry. Two hundred employees worked there on three, round-the-clock shifts. In 2009, Upper Big Branch produced 1.2 million tons of coal, about 3 percent of Massey’s total. The mine, like all of those operated by Massey, was nonunion.
The regulatory record revealed a widespread pattern of safety violations at the Upper Big Branch mine and an increasingly contentious relationship between its managers and government regulators. As shown in Exhibit C, government inspectors had issued an increasing number of violations over time, with a sharp spike upward the year before the disaster. These page 494data also showed that around 2006, management had begun to contest regulatory penalties rather than pay them. The state investigation reported the story that at one point Massey’s vice president for safety—an attorney—“took a violation written by an inspector, looked at her people, and said, ‘Don’t worry, we’ll litigate it away.’” Appealing the citations not only allowed the company to delay or avoid paying; it also blocked tougher sanctions, such as shutting down the mine.
Exhibit C: Safety and Health Citations, Upper Big Branch Mine, Assessed Penalties and Amount Paid, 2000–2009
Source: MSHA data, reported in the appendices of Industrial Homicide: Report on the Upper Big Branch Mine Disaster.
Miners testified that they were intimidated or disciplined if they complained about safety. When one foreman told his men not to run coal until a ventilation problem was fixed, he was suspended for three days for “poor work performance.” Another miner, who was killed in the blast, had told his wife that a manager had told him when he complained about conditions, “If you can’t go up there and run coal, just bring your [lunch] bucket outside and go home.” The father of a young miner who was still a trainee when he was killed at Upper Big Branch related his son’s experience to investigators. The young man had told his father that when he had expressed concerns about safety to his supervisor, he was told, “If you’re going to be that scared of your job here, you need to rethink your career.”12 Miners who were hurt on the job were told not to report their injuries, so an NFDL (non-fatal day lost) would not be recorded. A former Massey miner who testified before a Senate committee explained, “If you got hurt, you were told not to fill out the lost-time accident paperwork. The company would just pay guys to sit in the bathhouse or to stay at home if they got hurt.”13
Investigators found that the company had kept two sets of books at UBB, one for its own record keeping and the other to show inspectors. “If a coal mine wants to keep two sets of books, that’s their business,” the administrator for MSHA later commented. “They can keep five sets of books if they want. But they’re required to record the hazards in the official set of books.”14 Conditions that were recorded in the company’s own books—but not the official set—included sudden methane spikes, inoperative safety equipment, and other dangers.
(page 495)
The Upper Big Branch Mine
The mine also had a system in place, set up by its chief of security, to warn underground managers that an inspector was on the way—a clear violation of the law. A miner who survived the explosion later told Congress, “The code word would go out we’ve got a man [government inspector] on the property…. When the word goes out, all effort is made to correct the deficiencies.”15 A surviving miner testified:
Nobody shuts one of Don Blankenship’s mines down. It has never happened. Everyone knows when mine inspectors are coming, you clean things up for a few minutes, make it look good, then you go back to the business of running coal. That’s how things work at Massey. When inspectors write a violation, the company lawyers challenge it in court. It’s just all a game. Don Blankenship does what he wants.16
After the disaster, Blankenship stated, “Violations are unfortunately a normal part of the mining process. There are violations in every coal mine in America, and UBB was a mine that had violations.”
Causes of the Disaster
In the months following the tragedy at Upper Big Branch, three separate investigations—conducted by the federal MSHA, a commission established by the governor of West Virginia, and the United Mine Workers—examined the causes of the fatal explosion. All came to the same conclusion: that a spark from the longwall shearer had ignited a pocket of methane, which had then set off a series of explosions of volatile coal dust that had raced through the mine. Such events could only have happened in the presence of serious, systematic safety violations. Among the problems cited by the investigators were these:
· Rock Dust. Investigators found that the company had failed to meet government standards for the application of rock dust. As a result, explosive coal dust had built up on surfaces and in the air throughout the mine.
The state commission reported that the Upper Big Branch mine had only two workers assigned to rock dusting, and they typically worked at the task only three days a week and were frequently called away to do other jobs. Moreover, their task was often impossible because the mine’s single dusting machine, which was about 30 years old, was broken most of the time. Federal investigators later determined that more than 90 percent of the area of the mine where the explosion occurred was inadequately rock dusted at the time of the explosion. They also found that the area of the longwall where the explosion began had not been rock dusted a single time since production started there in September 2009. The presence of large amounts of floating coal dust in the mine was also suggested by medical evidence. Seventy-one percent of the autopsied victims showed clinical signs of black lung disease, caused by breathing airborne coal dust. Nationally, the rate of black lung disease in underground coal miners was around 3 percent.
· Ventilation. Investigators found that the Upper Big Branch Mine did not have sufficient ventilation to provide the miners with fresh, breathable air, and to remove coal dust as well as methane and other dangerous gases.
Upper Big Branch, like many mines, used a so-called push-pull system in which large fans at the portal blew fresh air into the mine, and a fan on the other end pulled air out. The state page 496investigation found that this system did not work very well at Upper Big Branch. The fans were powerful enough, but the plan was not properly engineered.
The push-pull ventilation system at Upper Big Branch … had a design flaw: its fans were configured so that air was directed in a straight line even though miners worked in areas away from the horizontal path. As a result, air had to be diverted from its natural flow pattern into the working sections…. Because these sections were located on different sides of the natural flow pattern, multiple diversionary controls had to be constructed and frequently were in competition with one another.17
Poor ventilation had likely caused methane to build up near the longwall shearer, providing the fuel for the initial fireball, investigators found.
· Equipment Maintenance. Investigators concluded that water sprays on the longwall shearer were not functioning properly, and as a result were unable to extinguish the initial spark.
After the disaster, investigators closely studied the longwall shearer where the initial fire had started. They found that several of the cutting teeth on the rotating blades (called “bits”) had worn flat and lost their carbide tips, so they were likely to create sparks when hitting sandstone. The investigators also examined the water nozzles on the shearer, which normally sprayed water onto the coal face during operation to cool the cutting bits, extinguish sparks, and push away any methane that might have leaked into the area. They found that seven of the nozzles were either missing or clogged. Tests found that the longwall shearer did not have adequate water pressure to keep the surface wet and cool. As a result, any small sparks thrown off during the mining process could not be extinguished.
In short, a series of interrelated safety violations had combined to produce a preventable tragedy. The United Mine Workers called the disaster “industrial homicide” and called for the criminal prosecution of Massey’s managers.
For its part, Massey had a completely different interpretation of the causes of the events of April 5. An investigation commissioned by the company and headed by Bobby R. Inman, its lead independent director, said that the explosion was caused by a sudden, massive inundation of natural gas through a crack in the mine’s floor—an Act of God that the company could not have anticipated or prevented. The company report stated:
… the scientific data that [Massey] has painstakingly assembled over the last year with the assistance of a team of nationally renowned experts so far compels at least five conclusions. First, a massive inundation of natural gas caused the UBB explosion and coal dust did not contribute materially to the magnitude or severity of the blast; second, although an ignition source may never be determined, the explosion likely originated in the Tailgate 21 entries, but certainly not as a result of faulty shearer maintenance; third, [the company] adequately rock dusted the mine prior to the explosion such that coal dust could not have played a causal role in the accident; fourth, the mine’s underground ventilation system provided significantly more fresh air than required by law and there is no evidence that ventilation contributed to the explosion; and fifth, MSHA has conducted a deeply flawed accident investigation that has been predicated, in part, upon secrecy, protecting its own self-interest, witness intimidation, obstruction of [company] investigators, and retaliatory citations.18
In a conversation with stock analysts six months after the disaster, Blankenship stated that he had a “totally clear conscience” and that he did not believe Massey had “contributed in any way to the accident.”19
The Upper Big Branch Mine
Discussion Questions
1) What were the costs and benefits to stakeholders of the actions taken by Massey Energy and its managers?,
2) Applying the four methods of ethical reasoning (utilitarianism rights justice and virtue do you believe Massey Energy behaved in an ethical manner?, Why or why not?,
3) Who or what caused the Upper Big Branch mine disaster and why do you think so?,
4) Who or what caused the Upper Big Branch mine disaster and why do you think so?,
Reference:
Lawrence, A., & Weber, J. (2022). Business and Society (17th ed.). McGraw-Hill Higher
Education (US). https://reader2.yuzu.com/books/9781265914769
image1.png
image2.png